Process-reliable mass production of knurling profiles
Modern coatings increase the service life of knurling rolls many times over compared to uncoated rolls.
Challenge
Rapid and unpredictable wear or breakage of the knurling roll leads to significant production problems. This can lead to defective workpieces and production downtime. The service life of the tools is a decisive factor for productivity and profitability.
Solution
Modern coatings reduce the friction coefficient of the knurling rolls and increase their hardness. This makes the tools more resistant to wear and tear and lasts significantly longer. A lower friction coefficient also leads to smoother and finer workpiece surfaces. This is particularly important for aesthetic applications where surface quality plays a central role
Coating options for knurling tools
DVA for tool steel with a high carbon content such as 1.1730 (C45W) or 1.2842 (90MnCrV8).
WC/C for chrome steels with a low carbon content such as 1.4301 (X5CrNi18-10) or 1.4305
TiN especially for knurling rollers when very clean knurling surfaces are required. Suitable for a wide range of materials.
DLC for the highest optical requirements for non-ferrous metals such as aluminum and copper alloys.
Practical example
With the uncoated HSS knurling roller from the competitors, a maximum of 40,000 knurling profiles could be produced.
The IFANGER knurling roller (see attached drawing) with DVA coating reliably produces 200,000 knurling profiles.
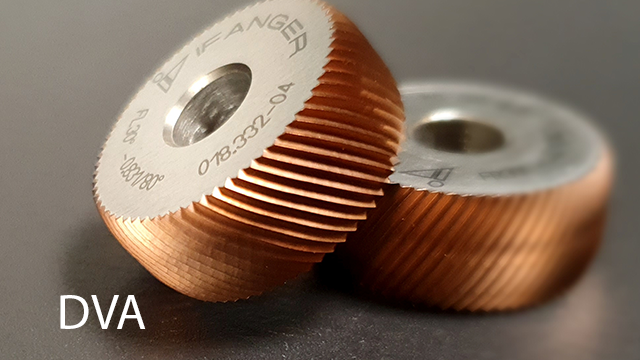
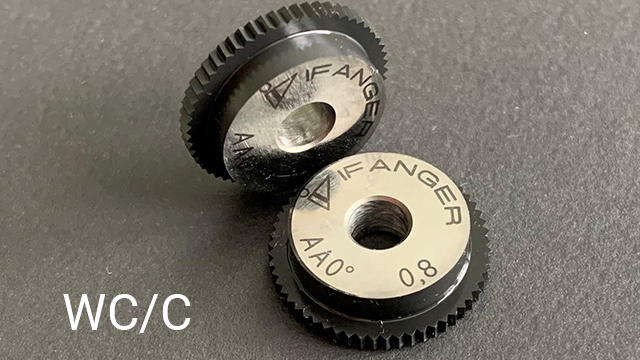
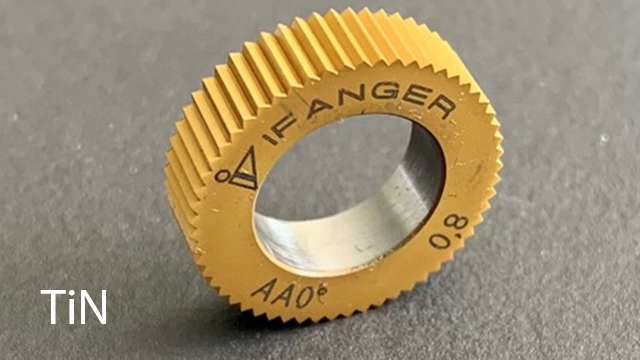
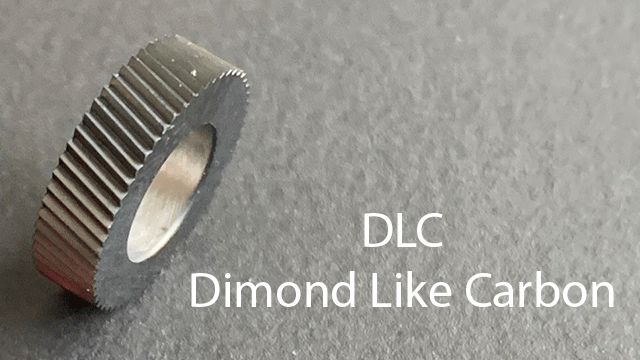