High-volume production of precise bores in austenitic chromium-nickel-molybden stainless steels (1.4401 and 1.4404).
This example shows how Swiss-MicroTurn tools can achieve the best results, especially when high surface qualities and process reliability are required.
Challenges
For large-scale production at ETSM SA, the objective was to achieve and guarantee a roughness (Ra) of 0.4 and a tolerance of ±0.0025 mm on a Ø7.85 mm over a length of 20 mm, all with efficient chip management. The parts were manufactured on a Citizen M32 sliding headstock lathe. The coolant (oil) came from the side without high pressure. Initial trials with a variety of boring tools from many well-known manufacturers produced unsatisfactory results with all the parts out of specification.
Problems
The first parts produced had a bad surface roughness (Ra), compromising the required quality and precision. Burrs were also found. The materials used, 1.4401 and 1.4404 (austenitic chromium-nickel-molybden stainless steels), added further complexity.
Solutions
To overcome these challenges, a methodical approach was adopted:
1. Tool selection: After several unsuccessful attempts, high precision IFANGER Swiss-MicroTurn were selected. These tools are designed for machining austenitic stainless steels or similar difficult materials, guaranteeing better performance and a surface finish that meets the requirements.
2. Optimized cutting parameters: the parameters were carefully adjusted to optimize speed, feed and depth of cut. This reduced vibration and improved surface quality.
3. Rigorous quality control: the quality & reliability of the tool were confirmed by the strict quality control implemented at every stage of production to ensure that every part produced met the specified tolerances and surface roughness.
The benefits
Thanks to these measures, production was able to meet the quality and precision targets set. Part quality and repeatability were excellent. The parts produced conformed to the specifications defined in the drawing below. Efficient chip management also helped to keep production running smoothly and without interruption. This success not only improved the quality of the finished products, but also reinforced the customer's confidence in the company's ability to meet stringent production requirements. In partnership with ETSM, our loyal partner for over 20 years, we took on a challenge that at first seemed a little daunting. Thanks to close collaboration and the expertise of our teams, we were able to overcome the obstacles and successfully achieve the objectives.
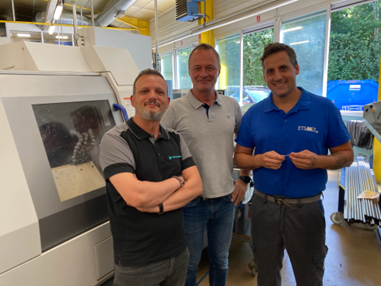
From left to right:
Angelo Muci (IFANGER Advisor), Philippe Meier (ETSM Director) and Christophe Wulliens (ETSM Bar Turning Manager), who celebrated 20 years with the company in 2024.